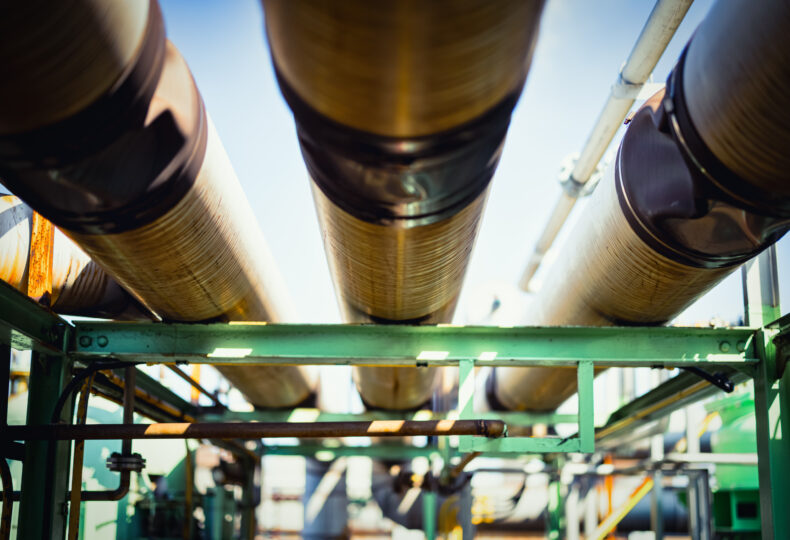
Tight clean room management:“I want to oversee a new active pharmaceutical ingredient from formulation through to manufacturing” – From the factory floors of intermediates for new drugs (Part 2)
We sat down for the second time with supervising manager of manufacturing Mitsusuke Hirono of Manac’s Fukuyama Factory, who works with pharmaceutical-related products, to learn about the behind-the-scenes details of daily efforts to meet strict regulations. During the ten or more years needed to develop new drugs, manufacturers of drug intermediates and active ingredients face many difficulties and obstacles. Mr. Hirono offered further details behind overcoming such challenges and facing the enormous pressure and stress inherent in the process.
■ What you can learn from this article ✔ In drug production, scaling up often causes new issues, making adjustments difficult. ✔ Thorough cleaning on the production floor is essential for quality assurance. ✔ Mr. Hirono’s dream is to market an API for a new drug developed by Manac. ■ Recommended Articles ・ “It’s useless…” Succeeding in bringing a gynecological investigational drug intermediate to manufacturing after a never-ending wait! From the factory floors of intermediates for new drugs (Part 1) ・ The secret behind “MANAC is bromine”/Defining what should be passed on to the next generation, as told by Fukuyama native factory chief ・ The story behind MANAC Shanghai’s first woman president in a chemical industry noticeably devoid of key women players
contents
Discrepancies that occur when scaling up
When manufacturing the intermediates and active pharmaceutical ingredients (APIs) of a new drug, production is carried out on a very small scale during the initial research stages. This is later advanced to a phase called commercial scaling, which produces the materials at a scale of thousands to tens of thousands of times larger than that of the research stages. When production is scaled up, reactions that were non-existent before may arise. Mr. Hirono explains that adjusting for these issues is the most difficult part of the process.
“For example, the amount of time it takes to heat a substance will increase relative to any increase in the amount of the substance used. If that substance produces impurities when exposed to heat, this increase in heating time will also increase the amount of impurities. Cooking works in the same way, since the time and amount of heat required for a small kitchen pot compared to a large cafeteria pot differs completely. We have to be able to achieve stable production even when the amounts are increased.”
Scenarios in which a market shortage of a certain drug occurs are unacceptable and would cost the company its reputation. Providing a steady supply of products, guaranteeing patients the drugs they need, can be described as a major mission of manufacturers of drug intermediates and APIs.
Washing and cleaning are “paramount” on the production floor
Production sites manufacture several products in succession. Specialized equipment is not always available for use. Any material that remains in the machinery from the last product will impact the next product that is produced. For this reason, it is “paramount” that washing and cleaning are carried out thoroughly and completely after the production of each and every product. This requires governmental inspection and client surveys over long periods to obtain evidence that guarantees product quality.
Additionally, the final manufacturing process takes place in a “clean room,” which controls fine air particles, temperature, humidity, and pressure. This room is tightly managed to prevent any contamination or foreign materials from being mixed into the product.
“The contamination of foreign materials can happen at any company if management is not maintained at a high standard. This is why we cannot let our guard down.”
The dream of manufacturing Manac’s own API for a new drug
“It’s my dream for a new drug’s active pharmaceutical ingredient, completely developed by Manac from formulation to manufacturing, to be released to the market.”
Manac’s prominence would rise rapidly if it released its own originally developed API for a new drug. This could also lead to new partnerships with other companies, and the start of new projects.
“I believe that Manac already has the technology necessary to accomplish this. However, it’s important that we first profit from our current products and position ourselves to handle new investments.”

Managing stress with music
Mr. Hirono views the standards imposed on the manufacture of pharmaceutical intermediates and APIs and their quality assurance as being based on cynicism. In other words, these frameworks assume people inherently do bad things, and aim to keep people from doing bad things.
On top of this framework, the process from research & development to manufacturing involves repeated advances and setbacks, taking years to produce results. It is a very stressful job. How does one overcome such pressure?
Mr. Hirono reports that the key to managing his stress is music. Not only has he enjoyed listening to music since he was young, he also plays bass, and was performing at a live house with a band he formed.
“I mostly play hard rock. During junior high, I thought 70s and 80s bands were really cool, and so I imitated those bands.”
Mr. Hirono concluded by sharing his hopes for the future.
“I think Manac still has a lot of hidden potential as a company. I want to contribute to the company in the pharmaceuticals area, but I believe Manac has great potential in other areas as well. I’m excited to see the development of new products.”