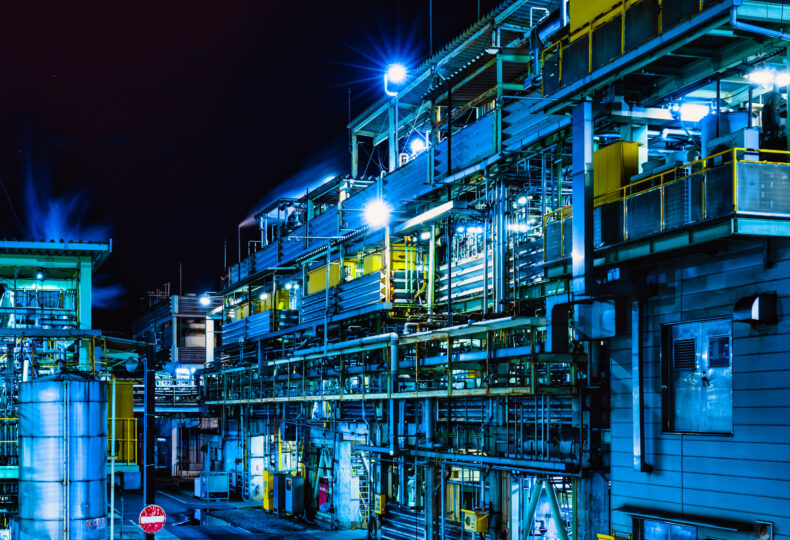
Methods of safely handling hazardous chemicals as told by Manac vice factory chief (Part 2)
Vice factory chief Kazuhiko Ohara, a manufacturing division supervisor of Manac’s Fukuyama Factory in Fukuyama, Hiroshima, Japan, continues unraveling the secrets behind factory safety initiatives in this second interview. By looking back at past incidents, Mr. Ohara strives to minimize mistakes and eliminate fatal errors as much as possible. We learned more about the key aspects of this endeavor.
■ What you can learn from this article ✔ Manac has an in-house fire brigade that swiftly responds and controls emergencies. ✔ Daily safety management and accident prevention are crucial for the continuity of factory operations. ✔ Employee mental health care, along with health management, contributes to workplace improvement. ■ Recommended Articles ・ Finding solutions through sharing an infinite number of “chilling, gut-wrenching” experiences – Behind the ensured safe manufacturing of more than 70 years since establishment (Part 1) ・ The secret behind “MANAC is bromine”/Defining what should be passed on to the next generation, as told by Fukuyama native factory chief ・ The art of controlling unexpected runaway chemical reactions — “young artisan” of contracted research taking on the challenge of developing pharmaceutical materials
contents
With only a tiny amount of liquid left…
What kinds of accidents have left an impression on you?
One of the worst accidents happened when we were inspecting the factory’s piping. We didn’t realize a small amount of a chemical liquid was left in the piping, which ended up spilling on one of the workers and causing an injury.
The spine-chilling emergency notification email
What measures are taken when that kind of emergency arises?
There are emergency alarms installed at each factory that notify the whole factory when the button is pressed. When the emergency alarm is activated, the in-house fire brigade is deployed immediately to administer first aid, secure safety, and bring the emergency under control. A notification email is sent to all related parties if an emergency occurs at the company on a holiday.
With this notification system, I receive an email on my phone that reads something like “An emergency has occurred at Fukuyama Factory” in the event of an emergency. Without knowing the details of what happened at that point in time, this kind of notification sends a chill down my spine.
What kind of measures are taken after an accident?
After an accident occurs, it is required that an urgent investigation into the causes is launched internally, permanent measures are established, and an operations improvement report is submitted to relevant government agencies, such as the fire department, the health care center, and the Labor Standards Inspections Office. It is crucial that we get to the root cause and ensure that a similar accident never happens again.
Improvement measures may be anything from equipment modifications to changes in manufacturing processes. It is of great importance that we take all possible measures to nip any risks in the bud.
Do you carry out any emergency drills that simulate the occurrence of accidents?
We hold around two or three emergency drills every year that simulate situations such as chemicals leaks and fires. You can’t expect to handle real emergencies without training, so it’s extremely important to prepare by carrying out drills.
We also have drills for natural disasters such as earthquakes and typhoons. We have evacuation sites and maintain at least minimum stores of drinking water and food for earthquakes and other disasters. One of the most problematic things during a natural disaster is power outages. A disaster like a typhoon can cause power outages and halt the operation of our facilities, which can create extreme instability. For this reason, it is important that we analyze the trajectory paths of approaching typhoons in advance and prepare our facilities to handle interruptions at any time.
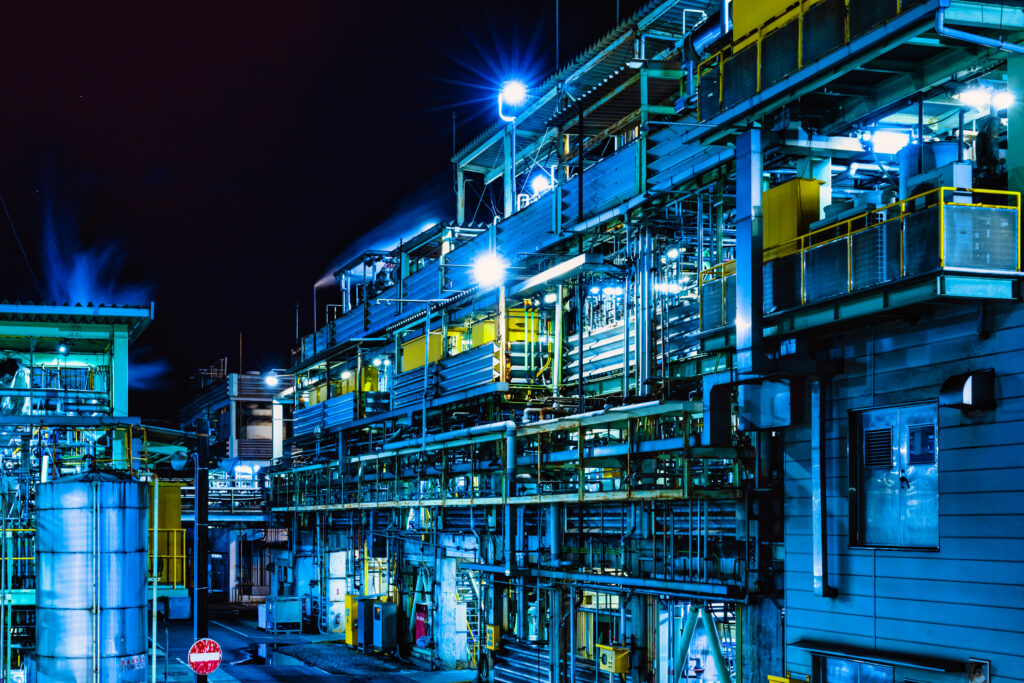
From managing chemical materials to caring for mental health
How would you describe the management of chemical materials?
Laws and ordinances regulate chemical substances, and management requirements have been growing more stringent in recent years. The criteria that determine what substances are regulated have also expanded, meaning that even certain materials that were recently available for general use are now being regulated or managed after the discovery of significant impacts on the environment or human health.
If regulations continue to tighten, we’ll have to either switch the regulated substances we use at Manac to other materials, or update our facilities to suppress the occurrence of such substances.
What precautions do you take when handling chemical materials?
We utilize systems that allow us to share information, such as the Globally Harmonized System of Classification and Labelling of Chemicals (GHS), which globally standardizes the indication of hazardous chemicals, and safety data sheets (SDS), which are information sheets for chemical products. We also ensure workers can maintain safe practices by carrying out employee training as required.
Is the maintenance of employee health included in “health and safety”?
Yes, of course. We carry out routine health checks twice a year and follow up on the results to ensure our employees can lead healthy lives. We also continuously carry out activities to improve the work environment. Instructors for mental health are also regularly invited to Manac to hold classes on mental health. Even for daily meetings and other regular tasks, we encourage employees to act as a sort of “gatekeeper” to achieve an even better workplace, staying vigilant toward the wellbeing of their coworkers and lending a hand or an ear whenever they notice something wrong.
Continuously approaching obvious, everyday matters deliberately and thoroughly
What would you say is the most difficult thing out of all the various duties you carry out?
I’d say it’s continuously ensuring that manufacturing operations are stable and maintained as planned, free of accidents, injuries, and equipment trouble. We’ve carried out manufacturing operations without any major accidents so far, but securing and maintaining safety as if it were a given is quite challenging. Halted factory operations due to a major accident would impact our ability to carry out manufacturing as well, so we cannot allow injuries or accidents to happen. That’s why we must work to maintain safety on a daily basis. We don’t do anything special for this, and it is instead essential that we continuously approach obvious, everyday matters deliberately and thoroughly.
One of the other most difficult things I handle is training. It’s important that we train personnel effectively, but this is also quite challenging. This is something I put a lot of thought into every year while handling training matters.
I believe Manac is a company where employees are free to assert their opinions, and a company where all you need is determination and inspiration to capitalize on your ideas. The future is in the hands of our younger employees, and I wish for them to continue demonstrating successes upon larger successes while protecting our culture of safety.