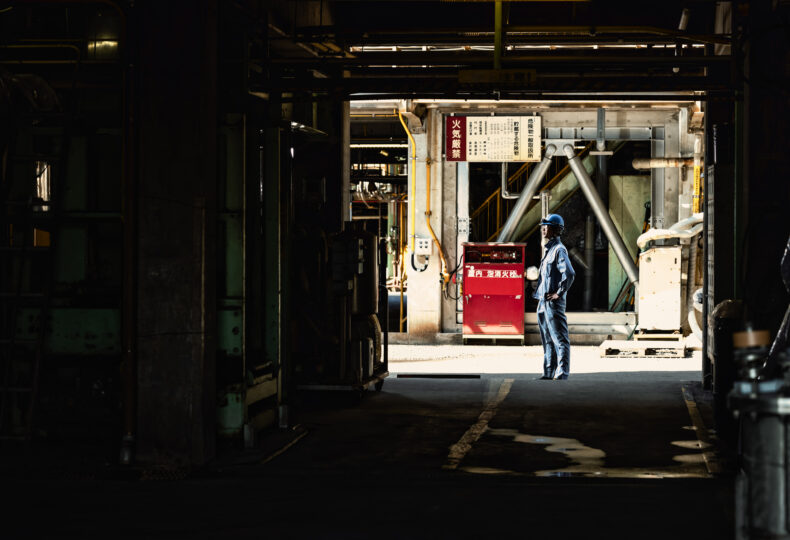
A seasoned professional with a “drone’s eye” — The philosophy of a chemosynthesis artisan of 40 years
Are there any rivers nearby your home? Rivers cannot easily be seen in their entirety from the ground. They flow from the swift currents of the river’s source deep in the mountains to its winding path down the hills, and finally downstream through your neighborhood. What we see of the river is merely a small fraction. If Manac’s research and development for chemical products was a river, Manac’s Kazumi Yoritaka could be described as a seasoned professional with a “drone’s eye,” able to peer over the river in its entirety, completely knowledgeable from its upper currents down through to its lower stream. His 40 years of experience lends to a wide field of view, able to spot difficult challenges in research and identify the key points to reaching the goal of commercialization.
■ What you can learn from this article ✔ Mr. Yoritaka uses his 40 years of experience to guide from research to manufacturing. ✔ Manac boldly entrusts young employees with responsibility, fostering their growth. ✔ Mr. Yoritaka succeeded in technical guidance overseas, overcoming cultural and language barriers. ■ Recommended Articles ・ From OLED to solar batteries, functional materials, and semiconductors, as told by the famous “catcher” of contracted research: “The difference between me and AI” ・ Driving semiconductor advancements with MANAC products – Developing the next-gen resist raw material “TIP” through a synergy of research and marketing ・ An essential for advanced semiconductors — A look at MANAC’s “TIP” as a next-gen resist raw material
contents
The road from marine microorganisms to chemosynthesis
Born and raised in Manac’s hometown of Fukuyama City, Hiroshima Prefecture of Japan, Mr. Yoritaka joined Manac in 1981 and was part of the research branch for 25 years.
“On the whole, I did the same kind of experimental research that I do now with organic synthesis as a university student. The research was for synthesizing antibiotics obtainable from marine microorganisms. After joining Manac, carrying out organic synthesis at a much larger industrial scale became my job.”
Gaining confidence during his fifth year at Manac
Around his fifth year at Manac, Mr. Yoritaka was assigned to develop chemical intermediates with compound structures containing halogen atoms for pharmaceutical products. While modest in size, Mr. Yoritaka created specialized equipment, produced test products from his first experiments, and collaborated with factories to proceed on to mass production.
“I don’t think I would’ve been able to gain the experience of carrying out an assignment from start to finish like this if I had joined a large corporation.”
Mr. Yoritaka explained that fully carrying out the entire process at a young age, including accurately understanding the important requirements for synthesizing a product, deciding equipment operating conditions, and providing a stable supply, gave him a great sense of confidence.
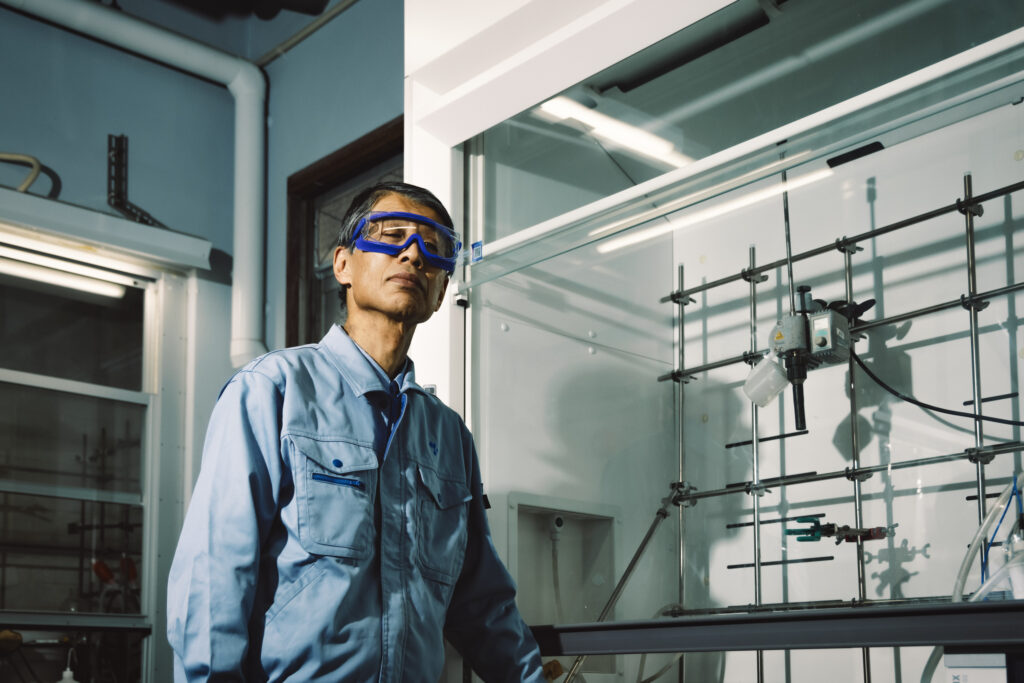
A company that completely entrusts younger employees
Entrusting younger employees completely with responsibility is a part of Manac’a culture that spans from Mr. Yoritaka’s early days through to today. With a well-achieved career himself, Mr. Yoritaka now coaches younger employees. “Our younger staff members are much more talented than I was at their age.”
As one grows older, it’s difficult not to criticize younger generations, and thinking “young people these days are just so…” or “my generation was much more…” However, Mr. Yoritaka reports that he has never had any such feelings.
The only complaint Mr. Yoritaka had for younger employees was said in a pet-phrase-type manner. “If things aren’t going well, speak up.” Mr. Yoritaka focuses on raising each individual’s abilities, limiting his interference to the minimum risk management required. “They’ll progress on their own as long as us older employees don’t get in the way.”
Crossing oceans to share about technologies
The sharing of knowledge and technology achieved through many years of work does not stop in the company. Mr. Yoritaka also provided guidance at a partner company in Nanjing, China, over the course of three years. At first, language and cultural barriers presented obstacles in certain situations, but Mr. Yoritaka tried several ways to overcome this.
First, he made concise diagrams illustrating chemical reaction processes and conditions. He then made sure to start his explanations with the conclusion and was careful not to use vague expressions.
“There are unspoken things that can be mutually understood between Japanese people, and there are times that communication is better facilitated by leaving things a little ambiguous. But I learned the hard way that these things don’t work outside of Japan.”
Mr. Yoritaka was careful to remember these points when he visited a company in Israel for a business deal for a brominating technology. This will continue to be crucial knowledge to apply when expanding business overseas as a company.
Applying downstream experience
Mr. Yoritaka’s journey traverses from the research branch to manufacturing. If we think of research and development as the upper and middle streams, the manufacturing line, which turns technology into products, is the downstream area that flows into the sea. Much hard work has gone into finding just how to quantify equipment operation rates and each product’s profit status at a factory of about 100 workers.
Taking into account the facilities used to manufacture products, such as the number of reactors, the volume capacity of each reactor, and the total floor area of the facilities, Mr. Yoritaka was able to gain a solid grasp of the factory’s status based on numbers.
With his experience from both research and manufacturing, on top of his experience overseas, Mr. Yoritaka is now in a supportive role for younger employees.
“We have trained several outstanding staff members that can handle any kind of chemical synthesis. I now stay behind the scenes, including for duties I’ve done in the past, and simply help to fill in any gaps in our daily work.”