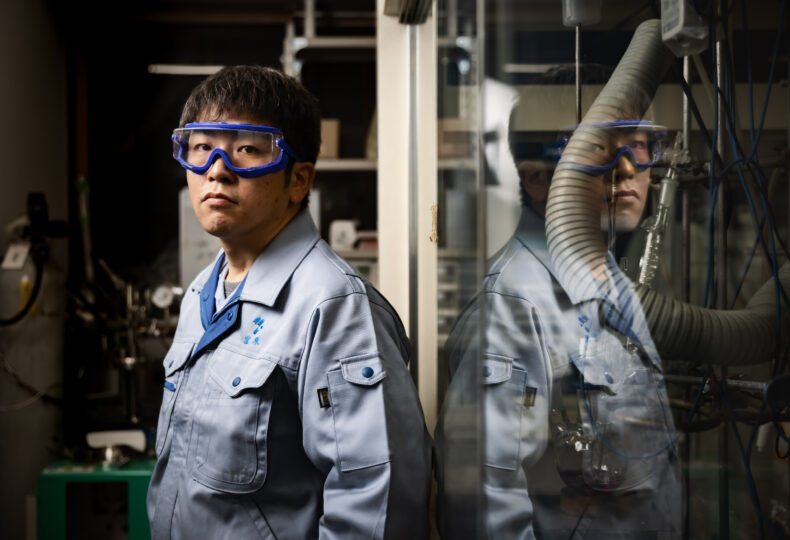
The art of controlling unexpected runaway chemical reactions — “young artisan” of contracted research taking on the challenge of developing pharmaceutical materials
Many companies commission Manac to produce compounds, for which it continuously conducts research and experiments to create compounds that meet client needs. Pharmaceutical Team member Hiroaki Miyahara of Manac’s Research and Development Center in Fukuyama, Hiroshima, Japan, researches raw materials used for pharmaceuticals. He is also in charge of the mass production implementation process for compounds at the factory of a joint venture (Iodo-Finechem Corporation) established with Godo Shigen Co., Ltd., one of Japan’s leading manufacturers of iodine. We asked Mr. Miyahara about his thoughts on compound manufacturing.
■ What you can learn from this article ✔ Manac develops synthesis processes for raw materials used in cancer-related pharmaceuticals. ✔ The production process was improved to control unexpected rapid heating during the experimental phase. ✔ The demand for Japanese pharmaceutical raw material manufacturers is increasing to avoid supply issues from overseas. ■ Recommended Articles ・ Responsibility and accomplishment as the engine of work / the younger members of the pharmaceutical manufacturing team (1) ・ Second year at MANAC and “put in charge, from raw material preparation through to final product” / the younger members of the pharmaceutical manufacturing team (2) ・ New business with diiodomethane – Aiming to realize SDGs by targeting API manufacturers with proprietary cyclopropanation reactions
contents
Developing synthesis processes for cancer-related pharmaceutical raw materials
What does your work at the research center entail?
We receive inquiries from clients asking if it’s possible to make certain types of compounds, and then we develop manufacturing methods that make it possible to make those compounds. The research and development center sits relatively upstream within Manac’s overall process.
Since I’m in charge of pharmaceuticals, I synthesize the components of investigational drugs and other pharmaceutical products. Recently I developed a manufacturing method for compounds for use as raw materials in cancer-related pharmaceuticals. You can successfully make a targeted compound in a beaker working in the laboratory, but that doesn’t necessarily mean it can be produced on a factory line. This makes testing at the factory an important job as well. On top of keeping manufacturing costs within the estimated budget, I take safety and environmental matters into consideration, checking for potential issues such as the occurrence of toxic gas.
Is it true that you take many business trips to Chiba Prefecture?
Yes, for about one week out of each month, I oversee the production of iodine compounds at a factory of a joint venture with Godo Shigen Co., Ltd., located in the village of Chosei just off the coast of Chiba’s Kujukuri beach. Iodine compounds are a specialty of both Manac and Godo Shigen.
The secret behind controlling rapid heating
Did production go smoothly?
That wasn’t exactly the case. When we started production tests for iodine compounds at the factory, unexpected chemical reactions occurred at the experimental stage, and the reacted liquids rapidly heated. Since there’s a risk of those kinds of liquids coming to a boil and erupting if left unchecked, we investigated ways to control such rapid heating.
What kind of measures did you take?
In addition to targeted substances, acid occurs as a byproduct when raw materials are mixed with catalysts and processed with chemical intermediates. While investigating the cause of this rapid heating, we found that this acid is necessary for intermediates to convert raw materials into the targeted substance, and that the expected chemical change won’t happen if the concentration of acid doesn’t reach a certain level.
The cause behind this runaway chemical reaction and rapid heating was the excessive buildup of intermediates before reaching the required level of acid concentration.
Learning from this experience, instead of adding all raw materials at once from the start, we tried adding just a portion of certain raw materials. To first produce more acid, we tried adjusting the amount and timing of added raw materials. Using this technique, we were able to suppress and control the occurrence of rapid heating.
That sounds like the work of an artisan, wouldn’t you say?
There was a time when we had trouble with catalysts, which we use to bring about chemical reactions. These catalysts would sometimes cause unwanted reactions after producing the targeted compound. Adding water would deactivate the catalysts, but the reaction with water would produce toxic gas. After discussing this issue with staff members of the research center, we solved the issue using substances other than water. Since Manac possesses technology and expertise for iodine and bromine compounds, the artistry I have gained from my senior colleagues has come in handy on a number of occasions.
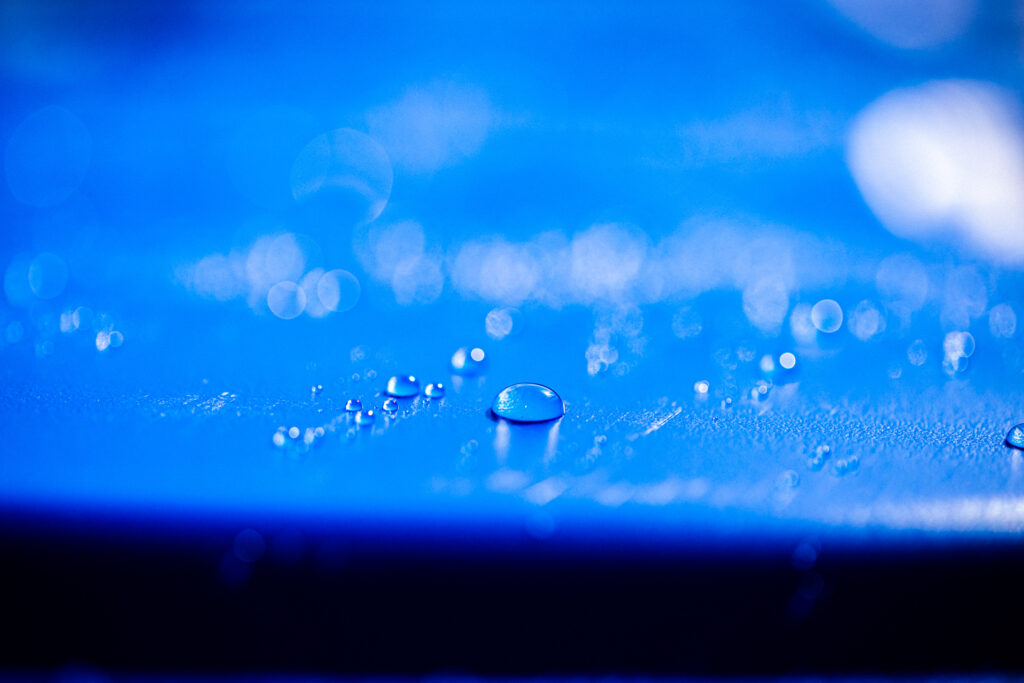
The rise of Japanese contracted manufacturers
How long does it typically take from the receipt of an order to the start of actual factory production?
It varies quite a bit between products. Out of the projects I oversee, the order for the project now I’m doing was received in 2014. The production method was established two years later, and factory production started in 2019, making the process five years. For pharmaceuticals, clients sometimes specify a development deadline since the timing of market introduction for such products is crucial for these companies. When it comes to pharmaceuticals, whether their raw materials can be produced or not can impact the health and lives of many patients.
What a great responsibility that must be.
Pharmaceutical companies also secure pharmaceutical raw materials from multiple manufacturers, including us. But in the case of non-Japanese manufacturers of raw materials, certain country risks may lead to a sudden supply interruption for any given reason, and so recently Japanese manufacturers have been on the rise. This makes sense because some companies have had to apply for and receive government approval to change the raw materials used in their pharmaceutical products due to such supply interruptions.
Pursuing high value-added materials unique to Manac
How rewarding would you describe your work to be?
It’s very rewarding to know that the compounds we’ve made will go on to help many patients as the raw materials used in cancer-related pharmaceuticals. Although chemical manufacturers don’t make final products that go directly to consumers, many products we use every day wouldn’t be possible without the raw materials we produce. We may be behind the scenes, but I know for a fact that our work is benefiting society.
What fields did you study as a university student?
My studies weren’t related to pharmaceuticals, but I conducted basic research in the field of organic synthesis. I conducted many experiments investigating what kind of changes compounds with a box-like structure would go through when exposed to light and electrical currents.
What are your goals now going forward?
Manac has amassed expertise regarding the handling of hazardous materials such as iodine and bromine. Some of the compounds we make are unstable, and so we have independently developed our own methods to stabilize and produce such materials. Leveraging the technology and expertise that we have grown, I want to create compounds with even higher added value from my own ideas.