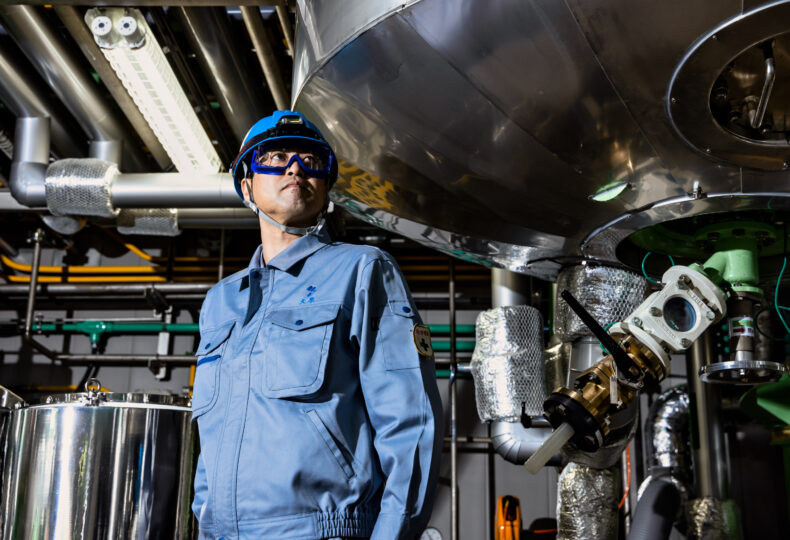
Finding solutions through sharing an infinite number of “chilling, gut-wrenching” experiences – Behind the ensured safe manufacturing of more than 70 years since establishment (Part 1)
One of the raw materials that Manac works with is bromine, which is a toxic chemical substance that requires great caution in its handling and management. Maintaining the safe handling of chemicals like bromine for stable manufacturing requires a solid understanding of the characteristics of the materials being handled, and a strict adherence to set rules. Initiatives toward health and safety shared properly among employees are crucial as well. We learned the secrets behind such management from vice factory chief Kazuhiko Ohara, a supervisor in Manac’s manufacturing division at the Fukuyama Factory in Fukuyama, Hiroshima, Japan. This story is a two-part series.
■ What you can learn from this article ✔ At Manac, strict management systems are in place to handle bromine safely. ✔ Workers wear full-body protective gear, and regular equipment inspections are conducted. ✔ Manac shares close calls to prevent major accidents before they occur. ■ Recommended Articles ・ The secret behind “MANAC is bromine”/Defining what should be passed on to the next generation, as told by Fukuyama native factory chief ・ Partner contract with Fukuyama City Football Club! The mastermind looks next to “raise the profile” ・ Responsibility and accomplishment as the engine of work / the younger members of the pharmaceutical manufacturing team(1)
contents
The meaning behind the “4Cs”
Mr. Ohara, could you tell us about your work?
I’m the vice factory chief of Manac’s Fukuyama Factory. We have around 160 employees working at the factory, including research and development staff members, as well as staff members from Manac’s manufacturing and environmental quality assurance divisions. My job is to ensure that the factory remains a pleasant workplace where employees can work safely and comfortably. To accomplish this, I keep an eye on a wide range of matters for the manufacturing division at the Fukuyama Factory, from improving operations to training personnel, as well as stable production, health and safety, and the management of fire prevention.
What kind of initiatives are being taken for health and safety at the factory?
We’ve established a health and safety committee that focuses on issues set as key initiatives based on factory policy to improve employee safety and the workplace environment. Working groups have formed within the committee, and each group proactively takes on efforts toward specific themes they have chosen.
What kind of themes are there?
Take, for instance, our initiative toward the “4Cs.” This stands for the four Cs found in the two phrases “close call” and “cause for concern.” This initiative works to facilitate the sharing of “close calls” that fortunately didn’t result in an accident, but were nonetheless gut-wrenching and chilling, as well as “causes for concern” for potential hazards. By bringing about the prompt sharing of such experiences and concerns among employees involved with manufacturing on the factory floor, this initiative works to prevent major accidents from occurring.
Collecting an infinite number of close calls
What kind of “close calls” have there been?
Some of the minor close calls we’ve had include tripping on the stairs and nearly taking a fall, and walking through a passageway and almost running into piping and other things in the way. We’ve also had close calls with staff members almost running into moving forklifts or trucks in the factory, and some who fell while loading and unloading cargo.
Other than that, we’ve had close calls that could have directly led to dangerous situations, such as nearly adding the wrong amount of a raw material (chemical substance), or almost exceeding precisely set pressure or temperature limits in a manufacturing process. We have an infinite number of these “close calls.” It’s imperative that these minor happenings are promptly dealt with to prevent major accidents from occurring, and that such events are shared with other departments to avoid repeating similar close calls elsewhere.
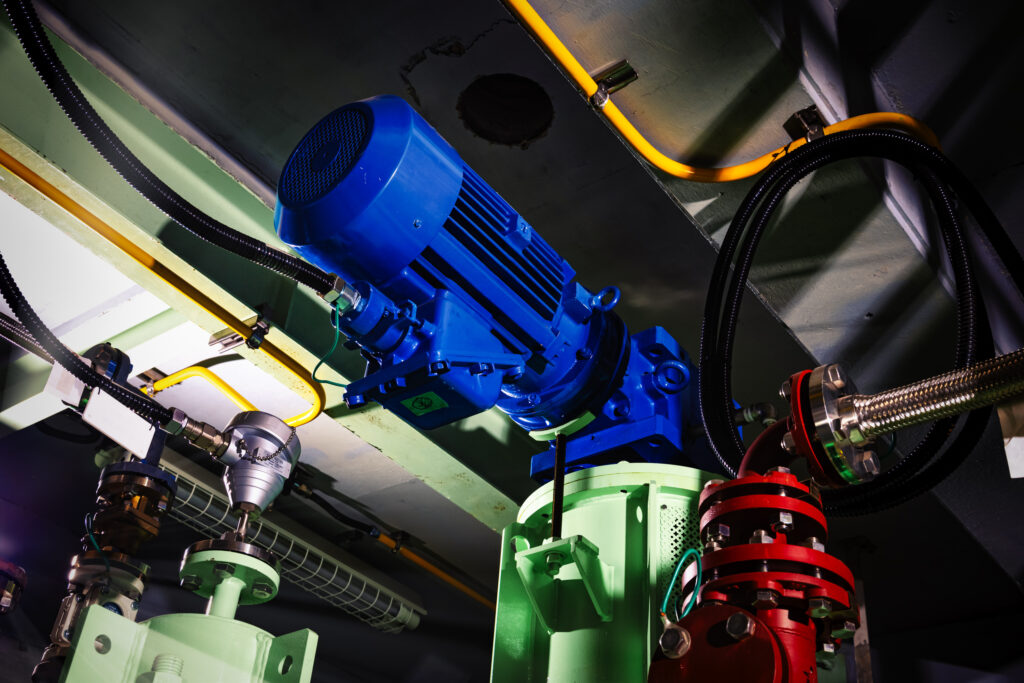
Workers who handle hazardous materials
You mentioned that toxic materials are handled at the factory. Is the management of this particularly difficult?
One of the most hazardous substances handled in large volumes at Manac’s factories is bromine, a highly toxic, reddish-brown liquid with a pungent odor. A bromine leak could be disastrous as the substance’s high volatility means it can diffuse and spread easily over a large area. Nothing short of extreme caution on top of extreme caution is acceptable for the handling and management of bromine.
Ensuring safety with full-body protective wear
The attention required is impressive. Is there any danger to the staff members?
Bromine can cause chemical burns and sores if it comes into contact with skin. Accidental inhalation can instantly cause similar irritations to the respiratory tract, leading to shortness of breath, and can cause death in severe cases. When working with bromine, factory workers prepare for the worst and wear full-body protective wear, including a face shield, protective mask, and protective gloves.
At Manac, we have a 5000-liter and an 8000-liter receiving tank for bromine. We receive bromine and transfer it to factories through pumps and the like almost daily. Our facilities undergo regular inspection and maintenance as part of our efforts to ensure the safe operation of our factories and to prevent any hazards to health.
*Part two of this story covers past issues and their solutions.