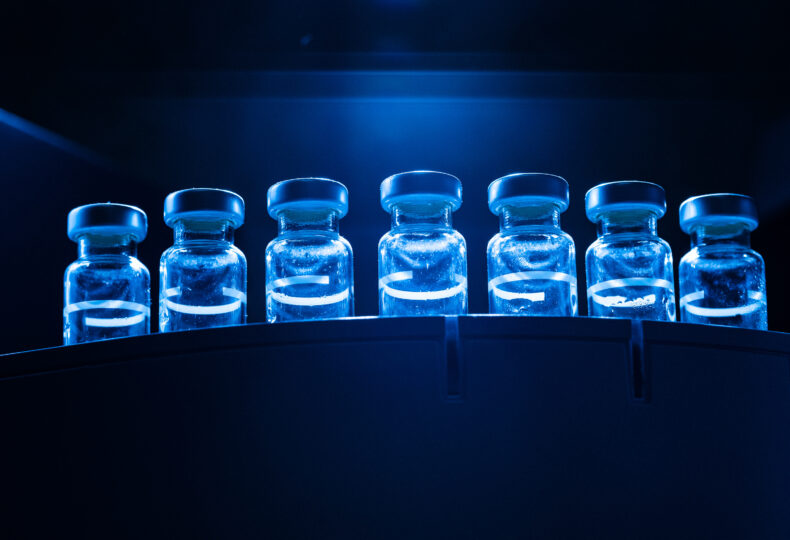
The a-ODPA polyimide monomer used for the IKAROS sailing spacecraft – The secret behind making specialized heat fusion possible
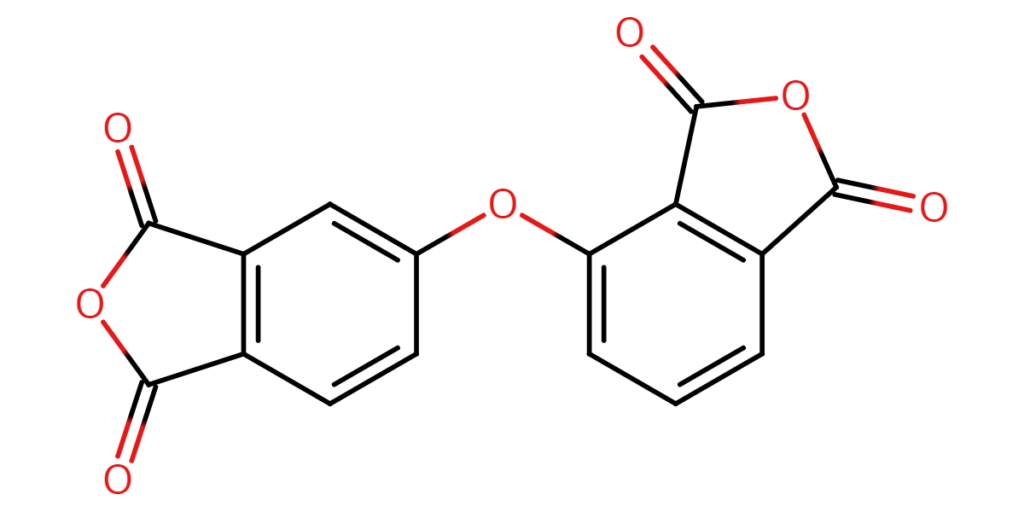
【CAS No.】50662-95-8
【Chemical name】4-[(1,3-Dihydro-1,3-dioxo-5-isobenzofuranyl)oxy]-1,3-isobenzofurandione
【Chemical formula】C16H6O7
Just like a sailboat catches the wind to sail the seas, imagine a spacecraft that catches sunlight to sail in space. It may sound like fantasy, but this kind of “sailing spacecraft” has already been made a reality. The IKAROS sailing spacecraft, launched by the Japan Aerospace Exploration Agency (JAXA) in May 2010, is one such spacecraft.
The sail used on IKAROS uses oxydiphthalic anhydride (ODPA), a compound developed by Manac. Just what is this compound that is being used for sailing spacecrafts? This article delves into the secrets behind this material.
■ What you can learn from this article ✔ IKAROS’s sail uses heat-resistant polyimide. ✔ a-ODPA softens at lower temperatures, enabling heat sealing. ✔ Heat sealing eliminates the need for adhesives, achieving lightweight sails. ■ Recommended Articles ・ The “sail” of spacecraft IKAROS made from specialized polyimide resin!
contents
Polyimide – the key player in realizing IKAROS
IKAROS is a small, solar-powered, experimental sailing spacecraft that utilizes a large-sized sail that measures 14 by 14 meters. The spacecraft moves in space by reflecting sunlight from the sail and using the energy obtained from the solar batteries embedded in the sail.
The idea of a sailing spacecraft like the IKAROS has existed since around 100 years ago, but the technology to produce a sail that could withstand the harsh conditions of space was out of reach. Compounds known as polyimides changed everything.
Polyimide resins were first commercialized in 1965, and possess the durable and heat-resistant characteristics needed for a spacecraft sail. This exceptional material we call polyimide made the realization of IKAROS possible.
A specialized polyimide that melts when heated
Resins such as polyethylene and polyimide consist of monomers, which are small compounds that form long structures.
Polyimide resins are formed by bonding the two monomers shown below, tetracarboxylic acid dianhydride and diamine, in an alternating pattern. There are numerous types of both tetracarboxylic acid dianhydride and diamine, and the final polyimide structure changes depending on the monomers used. (The reaction formula below is one example.)
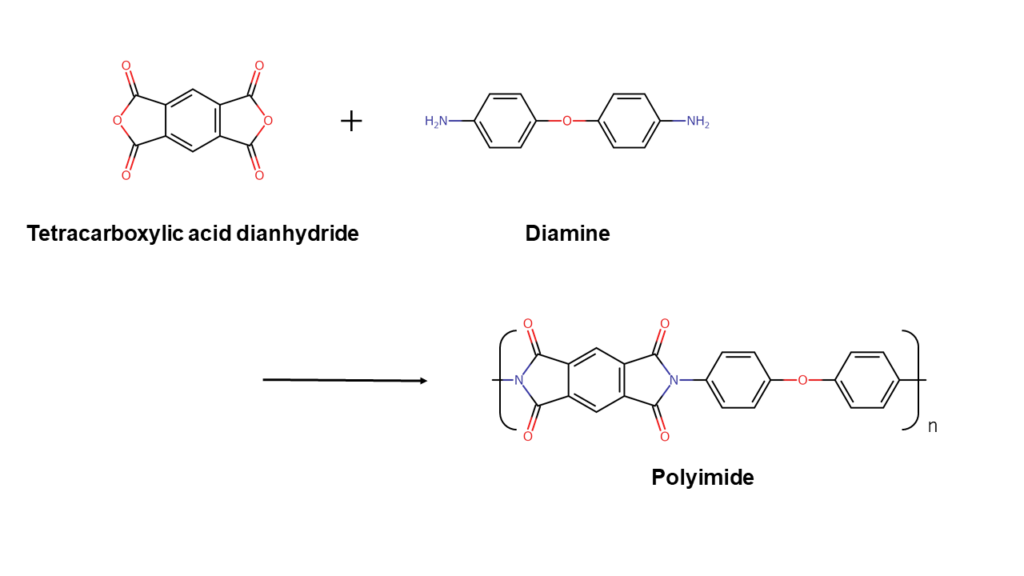
IKAROS uses two types of polyimides: a standard polyimide that can withstand heat of up to around 400°C without softening, and a specialized polyimide that softens when heat of around 266°C is applied.
The sail on IKAROS is made of multiple polyimide sheets that have been attached together. Using a polyimide that softens with the simple application of heat allows for the adhesion (heat fusion) of the polyimide sheets, which in turn achieves a lighter sail without the need to use glue. This means that IKAROS utilizes both standard polyimide and a specialized polyimide that allows for heat fusion.
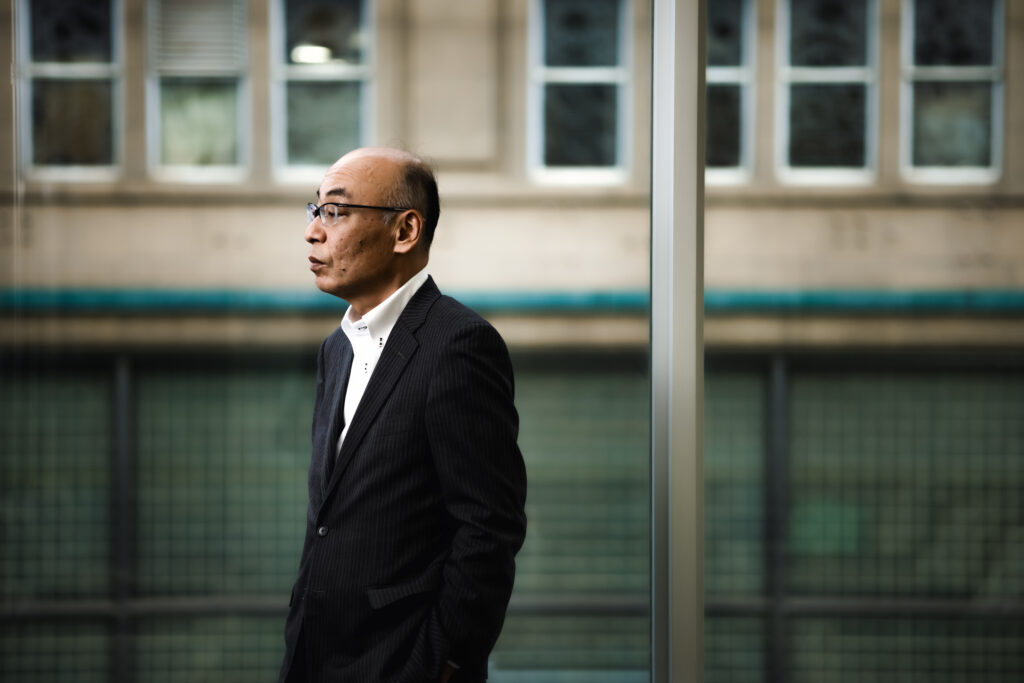
a-ODPA – the monomer behind the specialized heat fusion polyimide
For this project, Manac produced a-ODPA, the monomer that enables heat fusion in the specialized polyimide.
Manac also manufactures and markets a monomer used for polyimides called ODPA-C. The a-ODPA monomer used for IKAROS has a structure that can be described as a slightly bent version of the structure for ODPA-C.

While polyimides made with ODPA-C soften at around 280°C, polyimides made with a-ODPA soften at around 266°C. Since polyimides made with a-ODPA soften at a lower temperature, they are easier to use for heat fusion.
How a-ODPA enables heat fusion with polyimide
Why do polyimides made with a-ODPA soften at a relatively lower temperature? The answer lies in the bent structure of the a-ODPA monomer.
Resins like polyimides are formed by long repetitive chains of monomers. There is a force at play that pulls the links together (intermolecular force), and the bigger the contact area between the links, the stronger this intermolecular force becomes. This means that links in a straight chain have a large contact area and, therefore, a strong intermolecular force, while chains with bent links share a smaller contact area, resulting in a weaker intermolecular force.
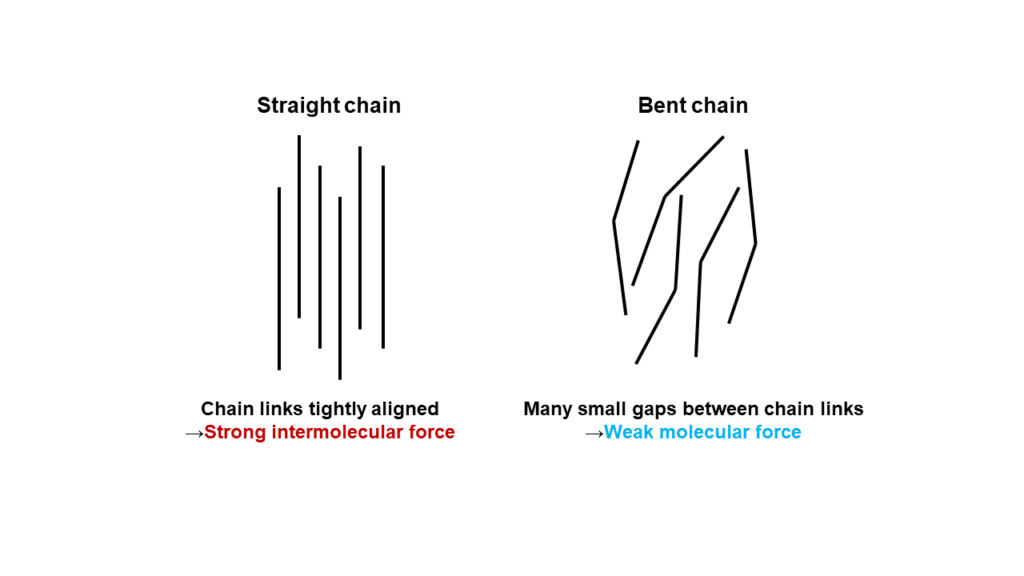
The chain links in resins normally separate and start moving around with the introduction of a certain amount of heat. This is the state that we describe resins as “soft.” The links in resins with a weak intermolecular force separate more easily than resins with a stronger intermolecular force, and therefore can be made softer at lower temperatures.
Since the a-ODPA monomer developed by Manac has a bent structure, the chains in polyimides made with a-ODPA also have similarly bent links. This creates a weaker intermolecular force between the chain links, and results in a polyimide that can be softened at around 266°C, a lower temperature than standard polyimides.
The enormous potential of polyimides
Compared to other resins, polyimide compounds are relatively new to the market, and features exceptional durability and heat-resistant properties as a material. There has yet to be a market established for polyimides that can be used for heat fusion, and their applications are expected to expand with the advent of new ideas.