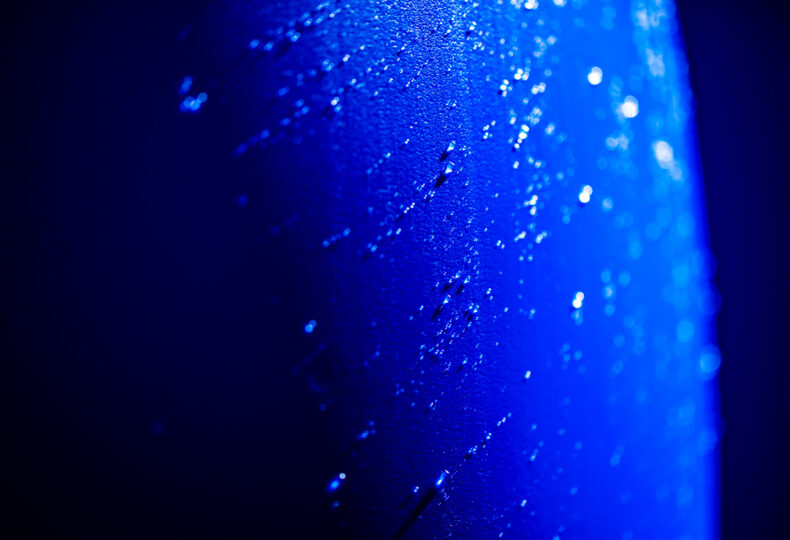
The “sail” of spacecraft IKAROS made from specialized polyimide resin!
A behind-the-scenes look at the making of a mere 2 kg over 1.5 years
A vessel sailing in space. It sounds like science fiction, but it is, in fact, a real story already being accomplished. IKAROS, a “sailing spacecraft” propelled by sunlight converted into energy, was launched by the Japan Aerospace Exploration Agency (JAXA) in May 2010, and has gained much attention. Many people were involved in this project, and Noriyuki Kawanishi is one of the unsung heroes who supported development. This is his behind-the-scenes story from 11 years ago.
The defining feature of IKAROS is in its giant solar sail measuring 14 by 14 meters. Thin solar batteries embedded in the sail power the spacecraft. The highly heat-resistant resin film made from the super-engineering plastic polyimide made this kind of sail structure possible. It was Mr. Nishikawa’s team at Manac that demonstrated its ability when developing the polyimide material for IKAROS.
How would you describe polyimide resin? It isn’t something you hear every day.
Polyimides are used a lot for semiconductors, and as far as everyday items go, they are crucial for smartphones. They also play a role in connecting electronic components in circuit and logic boards. Manac manufactures the major raw materials(polyimides monomers) vital to the production of polyimide resins.
■ What you can learn from this article ✔ Polyimide resin is highly heat-resistant and suitable for space use. ✔ Manac provided high-purity material to JAXA. ✔ Super-engineering plastics are expanding into various applications. ■ Recommended Articles ・ The a-ODPA polyimide monomer used for the IKAROS sailing spacecraft – The secret behind making specialized heat fusion possible
contents
Why use polyimides resin in space?
How did such polyimides come to be used in space?
Polyimide resins are highly heat resistant, with some types able to withstand temperatures of up to 500 degrees Celsius. On top of that, they don’t break down when exposed to chemicals as they possess a very strong molecular structure. JAXA approached us saying that they wanted to use a polyimide material for their IKAROS sailing spacecraft.
Specifically, what kind of work did you do?
Given the large size of the sail, the polyimide films usually used for applications such as electronic compounds were out of the question. It was necessary to make a larger polyimide film by attaching multiple polyimide films together in order to make the sail for IKAROS. The order we received was for the provision of the major raw materials required to make the polyimide contained in the adhesive needed to attach the films together.
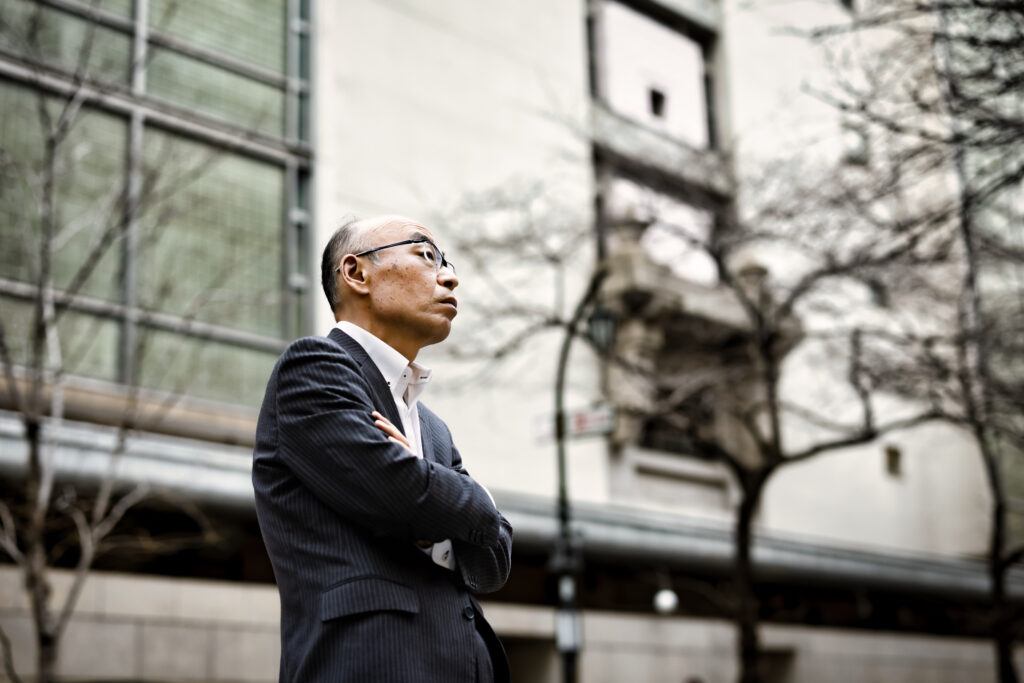
The challenge of maintaining strength while breaking polyimide down
It sounds quite complex.
Yes, as I mentioned earlier, polyimide resins are amazingly tough materials that don’t break down easily. In order to provide the major raw materials for a new material that would fulfill the necessary role as an adhesive, we needed to purposely break down the molecular structure of polyimide and get it to melt below 300 degrees Celsius.
That must have been extremely challenging.
There are no manuals that exist for creating this kind of material, and we struggled to achieve a material that had the physical properties required by JAXA. It took one and a half years of repeated trial and error to successfully make the material.
The “optimal solution” awaiting just over the horizon
What was the breakthrough?
The breakthrough came about in our work to increase the purity of the material. We worked hard to eliminate any impurity. A material with zero impurities would have a 100% purity level, and if we wanted to use this material for other purposes, 99.7% purity would be sufficient. For this material, we brought it up to 99.9% purity. That means it contained just 0.1% impurities. However, the more we increase the purity of the material, the less we can output by volume. We went through countless recrystallization cycles, repetitively melting and hardening the material, slightly increasing the material’s purity each time. The material we delivered to JAXA totaled a mere 2 kilograms.
JAXA must’ve been very happy when you delivered the high-purity material.
Not exactly…things got a little more challenging (chuckling). When JAXA proceeded to process the material, they reported that it didn’t quite have the performance they had imagined. We were hard-pressed with the deadline approaching. I believe it was an issue with something outside of purity, but JAXA worked very hard with us, and we managed to meet the deadline.
The potential of super-engineering plastics
The applications of polyimide resins, also known as super-engineering plastics, are gradually growing in number year by year. Other than electronic components, they have a wide variety of usages, including in films, coating agents, and heat-resistant coating materials, which are used in components for cars and trains. Polyimide resins have even been used in the process of artificially culturing cells. With ingenuity and ideas, the applications for polyimides are likely to continue expanding.